Advanced Powder Bed Fusion Materials for 3D Printing
Rilsan® Invent PA11: High Performance Material for Powder Bed Fusion
Rilsan® Invent PA11 (polyamide 11) is a standout powder bed fusion material, offering a range of high-performance, 100% bio-based powders designed specifically for the powder bed fusion process. Parts 3D printed with this powder bed fusion material not only showcase superior mechanical properties and weight savings compared to traditional PA12 (polyamide 12) but also boast exceptional impact resistance, along with higher ductility and elasticity.
Key benefits
The material of choice for sustainable series production
-
Superior performance and lower environmental impact compared to PA12
-
Easy to print
-
Advanced bio-circular material – 100% Bio-based and recyclable
-
Excellent resistance to oils, fuels and hydraulic fluids
-
Excellent Impact resistance
-
Superior Elasticity & ductility and fatigue resistance
-
Food contact statements available upon request (EU, FDA)
-
Cosmetic packaging statement available
-
USP Class VI compliant
DATA - Rilsan® PA11
Advanced Bio-Circular (ABC) Materials
Arkema is a pioneer in amino 11 chemistry. Our flagship Rilsan® PA11 elastomers have a proven legacy in meeting some of the world’s most demanding material challenges. This chemistry is derived from the castor bean, a sustainable, renewable crop that does not compete with food and does not cause deforestation. These are not "just" bio-based materials, however. They are truly advanced polymers that ultimately help the world reduce its carbon footprint... a carbon footprint that is further reduced when these ABC polymers are recycled & reused.
Don't let the common misconception about bio-based materials fool you when it comes to 3D printing! That's right, the backbone of Rilsan® PA11 is 100% based on a feedstock of castor oil AND there is no compromise in performance when compared to its closest relative, non-bio-based PA12. Learn more about our Pragati Initiative for sustainable castor farming in India here.
Impact resistance
3D printed Rilsan® PA11 parts can pass the interior part crash test for automotive applications, an extreme situation that most other 3D printed materials fail. Due to this incredible impact resistance PA11 also passes the safety standards for bicycle helmets, and is being embraced by the cycling community, as seen in the HEXR example above.
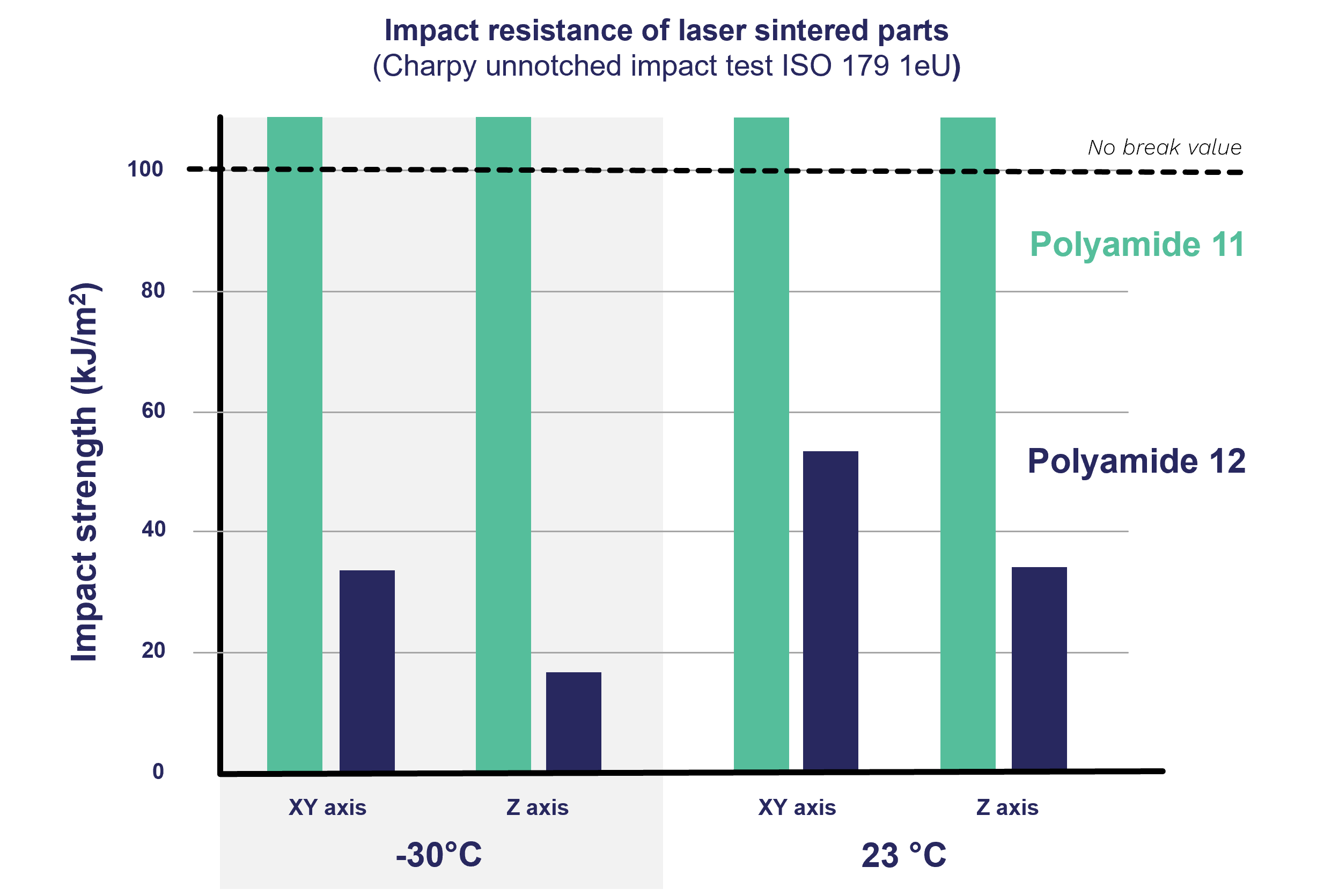
Stress-strain curve
The improved ductility of PA11 compared to PA12 allows designer to design thinner and lighter parts while using less material. The flexibility and durability of the material helps improve the lifetime of the part, yet if a failure does occur, the ductile breaking mechanism creates a safer environment compared to a brittle fracture seen in PA12 that could send dangerous shards into the air.
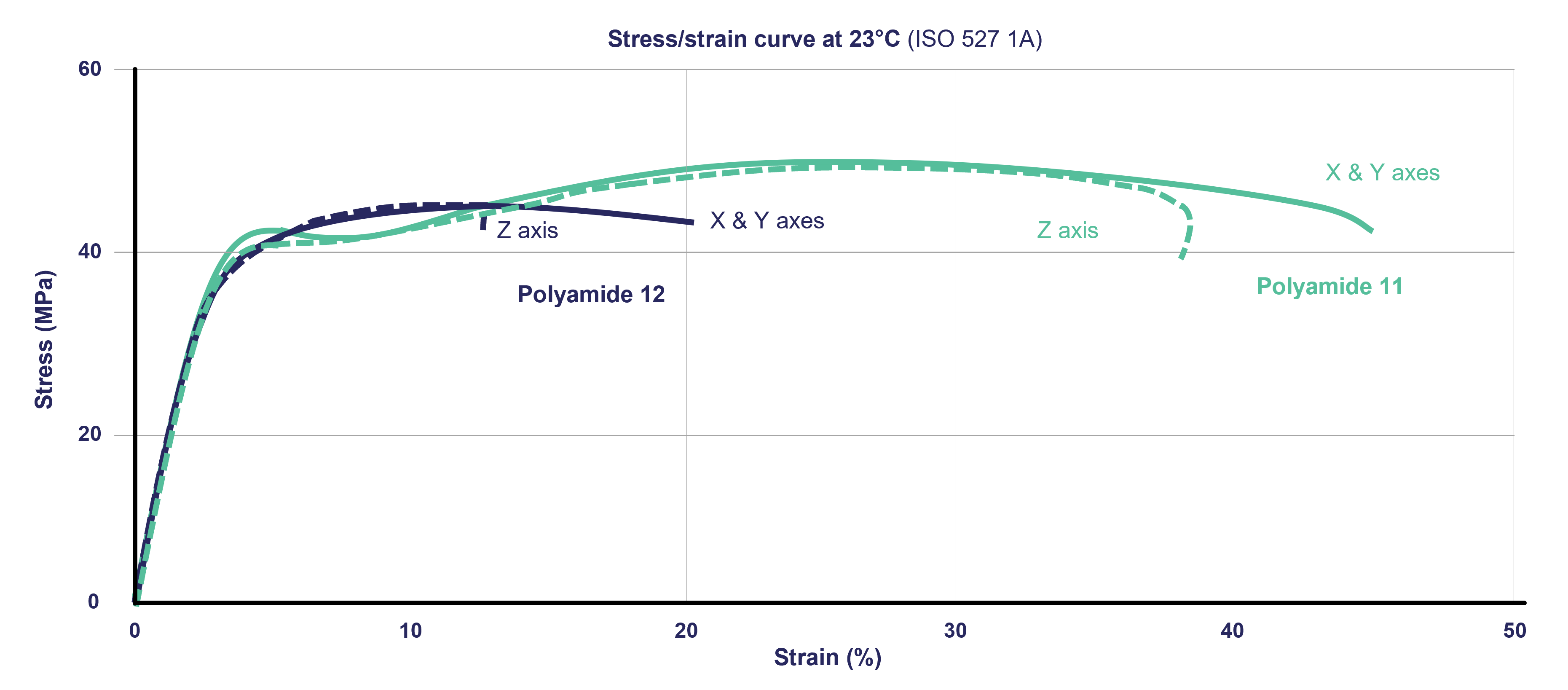
Fatigue curve
The graph below illustrates how a PA11 printed part under static load will maintain its mechanical strength over time compared to PA12 where we have observed up to 60% lower performance compared to PA11. This fatigue resistance is great for applications like the Bowman Rollertrain™ bearing cage shown above.

Kepstan® PEKK: Advanced Powder Bed Fusion Materials for Metal Replacement
Kepstan® PEKK (PolyEtherKetoneKetone) represents the cutting-edge in the PAEK (Poly-Aryl-Ether-Ketone) family, positioning itself as an ideal candidate for metal replacement within the realm of powder bed fusion materials. This latest addition shines in applications demanding very high service temperatures, unparalleled chemical resistance, and superior fire retardancy. As a standout among powder bed fusion materials, Kepstan® PEKK is engineered to meet the rigorous requirements of industries seeking to leverage the benefits of 3D printing technologies for producing components that traditionally relied on metal, thus offering a transformative solution for advanced manufacturing processes.
Key benefits
The material of choice for metal replacement
-
Bringing cost saving solutions compared to subtractive technologies
-
Commercially available solutions for both amorphous or semi-crystalline parts
-
Easier to print than PEEK - Minimal part warping in FFF, higher recycle ability in SLS
-
High modulus and strength
-
Outstanding high temperature performance
-
Inherent flame resistance, low smoke generation, and toxicity
-
Excellent chemical resistance (oils, fuels, Skydrol, and hydraulic fluids)
-
Outstanding mechanical properties; wear, compression and impact
-
High dielectric strength and good insulating properties
Pebax® Rnew® Elastomers: Revolutionizing Powder Bed Fusion Materials
Pebax® Rnew® Invent elastomers represent a remarkable advancement in the field of powder bed fusion materials. These elastomers stand out for their exceptional versatility, combining extreme lightweight properties with unparalleled flexibility. Pebax® Rnew® materials excel in fatigue resistance, impact durability, and offer an unmatched energy return when compared to traditional materials such as TPU. Their superior performance characteristics make them a preferred choice for industries looking to leverage the benefits of powder bed fusion technology, offering innovative solutions for a wide range of applications.
Download Pebax® Rnew® Thermoplastic Powder for Powder Bed Fusion Brochure
Key Benefits
The material of choice for flexible and durable applications
- Easy to print
- Superior performance compared to TPU
- Partly bio-based (grades starting at 30%+)
- Excellent elastomeric properties and fatigue resistance
- Superior flexibility at low temperature
- Extremely lightweight
- Excellent energy return
- Unique soft-touch feeling for raw parts
Orgasol® Invent PA12: Enhanced aesthetics & reduced cost per part
Unlock the full potential of PBF technologies with Orgasol® PA12 powders, designed to produce stunning parts at the lowest cost per part.
Orgasol® PA12 powders are a natural polyamide 12 specifically developed for 3D printing. Thanks to its unique particle shape and narrow particle size distribution, Orgasol® powders are the perfect material for the prototyping of small, complex parts, which display excellent contour resolution, yielding an incomparably smooth surface with no post-processing. Due to its unique, patented polymerization process, Orgasol® Invent Smooth powder has outstanding viscosity stability and excellent recyclability with a low refreshing factor.
Download Orgasol® Thermoplastic Powder for Powder Bed Fusion Brochure
Key benefits
- Game-changing cost efficiency thanks to unmatched powder recyclability
- Superior aesthetics thanks to powder spherical shape
- Zero-waste production achievable
- Increase reliability and repeatability
Game-changing cost efficiency thanks to unmatched powder recyclability*
Depending on the technology, part geometry & possible nesting density, one can achieve up to 50% savings on variable costs with Orgasol® PA12 compared to a standard PA12. Reach out to us to quickly evaluate your business case.
Superior aesthetics
Thanks to the Orgasol® PA12 spherical shape and narrow particle size distribution, the printed parts show outstanding aesthetics without costly post-processing.