Arkema wants to work with its customers on each side of the supply chain – those who want to recycle their polymers, and those who wish to purchase partially recycled grades. Our focus is on polyamide 11 and polyamide 12 resins, PEBA elastomers, and PVDF fluoropolymers.
Arkema acts as a kind of “match-maker” in terms of sourcing materials to be recycled and matching those materials with customers who desire partially recycled grades with a more favorable LCA profile.
Arkema’s recent acquisition of Agiplast, a high performance polymer recycler/ regenerator with a long history of high performance polymer re-engineering, recompounding, and re-certification, adds a new dimension to our traditional offer. The time is now.
Step into the loop™ and watch the Virtucycle Program video!
The Virtucycle® program is a partnership program offered to Arkema’s high-performance polymers customers and downstream users.
The program enables our partners to “step into the loop” by providing polymer for reprocessing or to source new materials with minimum recycled content and no compromise in performance
We collect your materials
We collect injected or extruded scraps, powders, parts and granules of long-chain polyamides (PA11, PA12), Peba thermoplastic elastomers and PVDF. The Virtucycle® Program sourcing team is available to evaluate the potential of your material for recycling at Agiplast Recycling Center. Arkema has dedicated expert scientists to meticulously analyze the raw material and recycled polymers to ensure the highest quality.
Pre-Consumer materials 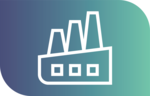
Materials that have been industrially processed but not turned into final products (so, usually scrapped)
Post-Consumer Materials
Materials have been industrially processed and used as final products in end-use applications
Certified recycled polymer grades
We provide recycled polymer grades certified through independent certifications. We guarantee that our recycled high-performance materials contain a certified minimum recycled content and have properties similar to virgin materials.
Arkema obtained its recertification of our enlarged certified recycled range from SCS Global Services in June 2024. More than 26 references were certified for recycled content by SCS Global Services after conducting a thorough eligibility audit of our production and suppliers. Our certified recycled offer, part of our Virtucycle® program, covers PA11, PA12 and PEBA containing from 30% to 95% minimum recycled content.
Three models of collaborating for your polymer recycling project
The recycling loop options
An important aspect to understand is closed loop vs open loop recycling models. At Arkema, we can facilitate and support both. The open-loop commitments often allow a more widespread effect on overall circularity on a global scale.
Closed-Loop: Items (and perhaps their recovered materials) are recycled into similar items for similar applications
Open-Loop: Items (and perhaps their recovered materials) are recycled into dissimilar items for different applications
|
Articles
Case studies
White papers
in Resources
Materialise and 3D printing powder recycling
Materialise, a leader in 3D-printed eyewear and promoter of sustainability in 3D printing, is committed to reducing its carbon footprint by 50% by 2025. For 3D printing powder that can no longer be used in the additive manufacturing process, Materialise works with Arkema's Agiplast recycling site to turn this powder into pellets for injection molding. Arkema has supplied long-chain polyamides to additive manufacturing for over 20 years and is proud to partner with Materialise to make powder bed fusion technology even more circular by recycling end-of-life powder.
On Running
Arkema collaborates with the Swiss sportswear manufacturer On who designed and launched the world’s first bio-based polyamide 11 shoe, fully recyclable, and sold using a monthly subscription model. These innovative shoes are made with Advanced Bio-Circular Rilsan® polyamide 11 derived from sustainable castor beans and as a leading supplier to the high-performance footwear market.