Kepstan® PEKK polymers
Ultra-Performance thermoplastics
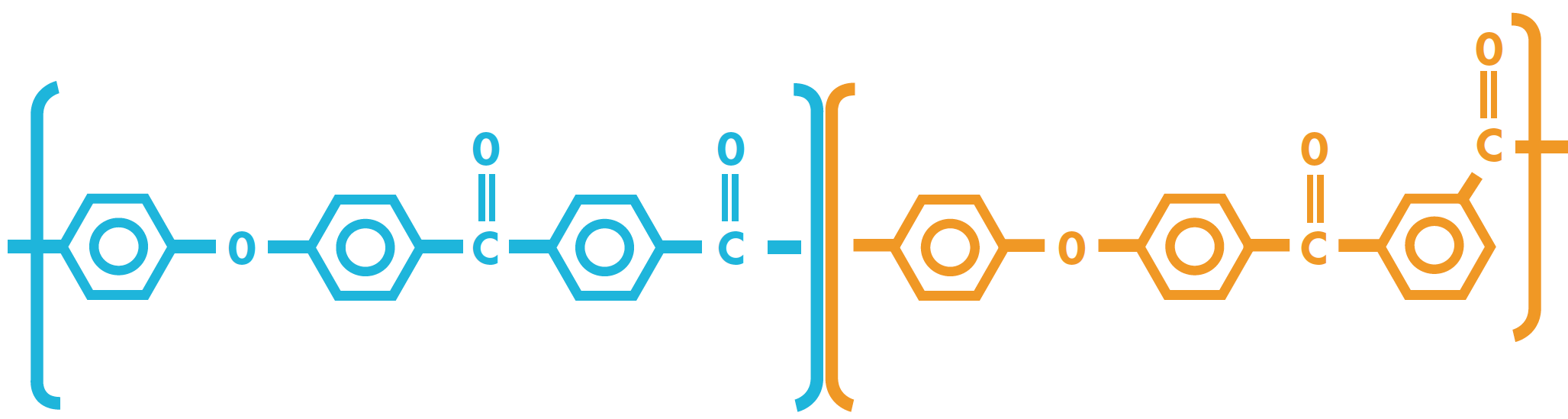
Polymer Performance
Kepstan® PEKK polymers are designed for applications requiring extreme performance:
•Outstanding Continuous Use Temperature (CUT) 250-260°C
•Excellent Mechanical Strength: Tensile, Compressive, Impact
•Excellent inherent Flame Smoke and Toxicity (FST) properties
•Exceptional Chemical Resistance
•High Dielectric Strength at ambient and elevated temperatures
•Tremendous Barrier properties (CO2, H2S...etc.)
•Outstanding control of Wear-rate and Coefficient of Friction (COF)
Three Different Series of Grades
Series | T/I Ratio | Melt Temperature (°C) | Glass Transition Temperature (°C) | Crystallization Speed | Typical Process |
---|---|---|---|---|---|
8000 | 80/20 | 358 | 165 | Fast / Semi-Crystalline | Injection Extrusion |
7000 | 70/30 | 332 | 162 | Medium / Semi-Crystalline | Composites Thermoforming Films |
6000 | 60/40 | 305 | 160 | Slow/Pseudo-amorphous | 3D Printing Powder Coating |
Find your material grade
Tailored Processibility
Unlike some other members of the PAEK (polyaryl-ether-ketone) polymer family, Arkema's Kepstan® PEKK polymers are highly customizable in terms of performance. Arkema achieves this customization or fine-tuning by carefully balancing the ratio of terephthalic ("T") and isophthalic ("I") monomers. Controlling this "T/I" ratio allows Arkema to produce grades with a range of crystallization rates and melt temperatures depending on the targeted method of final part production as well as the intended final use of the part itself.
Another dimension of polymer design is Arkema's tailored molecular weight control - allowing grades with highly specific melt volume indexes (from highly fluid to highly viscous).
These grades are then optionally filled with performance enhancing additives such as glass or carbon fibers, or carbon nanotubes.
The result is a portfolio of grades that may be extruded, 3D printed (selective laser sintering and fused filament fabrication), powder coated, injection molded, rotomolded, or impregnated in unidirectional composite tape fibers. Certain grades produced by certain processes may be even further optimized by careful choice of post-treatment or annealing conditions.
Amorphous or Semi-crystalline Kepstan® PEKK Powder Coatings
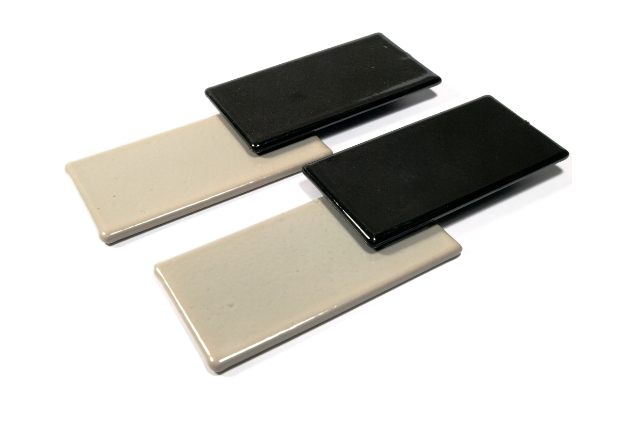
Global Supply
Kepstan® PEKK resins are manufactured in the USA and France. They are manufactured, marketed, and serviced as part of Arkema's High Performance Polymers business unit.