May 17, 2023 - 5 min
Lowering the environmental impact of waterproof & breathable membranes
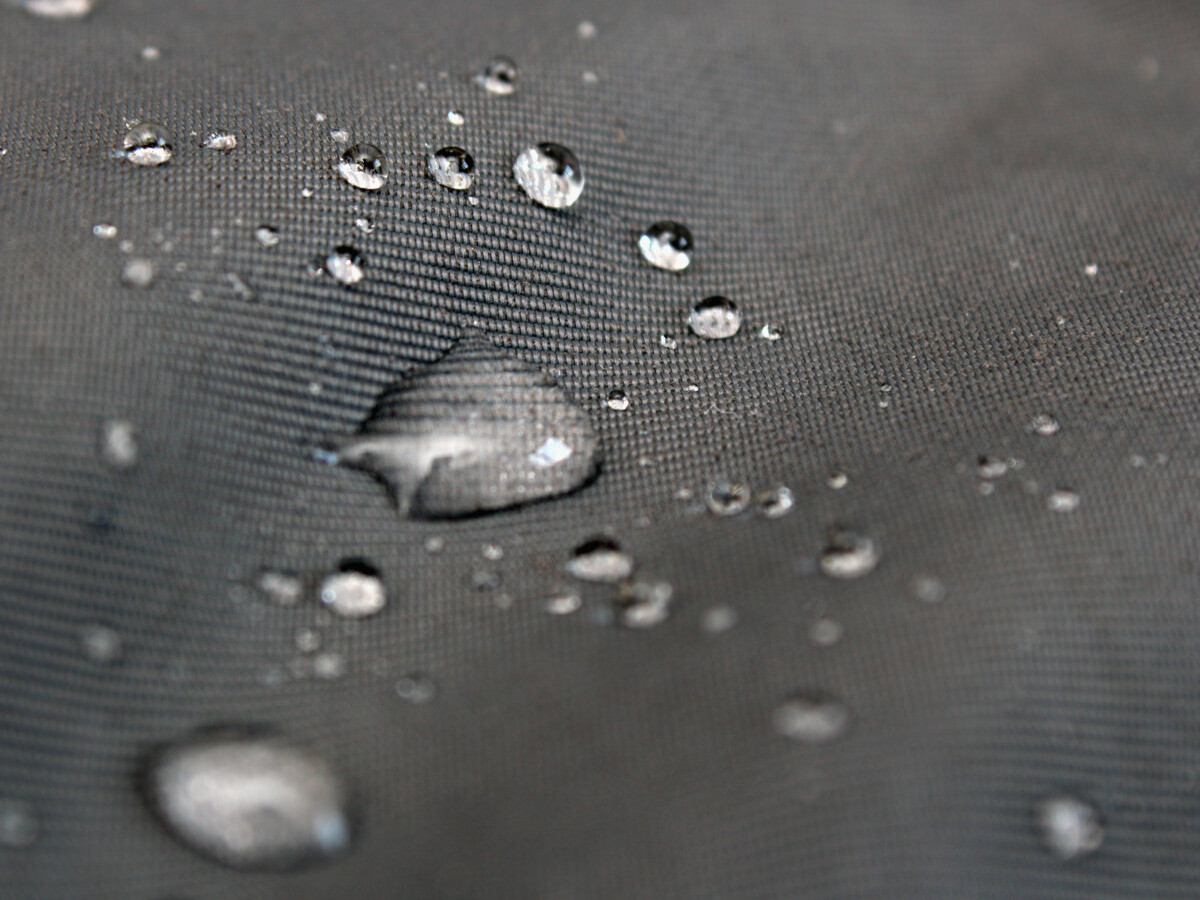
Breathable membranes have redefined comfort, performance, and protection in sports apparel, enhancing athletes' experiences and pushing the boundaries of their achievements. Following global trends related to sustainability, the market demand for lower carbon alternatives to conventional breathable membranes has never been stronger.
Arkema is ready to support this demand thanks to its bio-based Pebax® Rnew® range of materials, combining high performance and preferred sustainability profile.
What are waterproof & breathable membranes ?
Breathable membranes work on the principle of diffusion, allowing water vapor to pass through while blocking liquid water. This unique functionality enables them to regulate temperature, reduce sweat accumulation, and enhance moisture management, thereby enhancing athletes' comfort and performance.
How do the membranes work ?
Two technologies for waterproof & breathable membranes are available : microporous and monolithic.Microporous membranes feature tiny pores that allow moisture vapor to escape while preventing water droplets from entering.
On the other hand, monolithic membranes take advantage of the presence of hydrophilic groups wihin the membrane material to transfer water vapor molecules pass through the membrane yet preventing water to penetrate thanks to the unaltered surface.
What are the current challenges for waterproof & breathable membranes ?
The delicate balance between breathability and waterproofness remains a constant challenge. Ensuring that the membranes offer sufficient protection against external elements while allowing optimal moisture management and transfer. Durability and long-term performance are critical aspects as well : sportswear undergoes rigorous use, and require consistent functionality and durability over time to gain athletes' trust.Furthermore, reducing the environmental impact of breathable membranes is crucial to ensure their long-term sustainability. It is imperative to explore alternatives with a lower impact, such as bio-based or recycled materials, that minimize carbon emissions and resource depletion.
Arkema is driving the change to more sustainable waterproof & breathable membranes
No compromise on performance with our bio-based Pebax® Rnew® breathable film solution for monolithic membranes.A Low-Carbon Alternative to Traditional Membranes
How can we lower the carbon footprint of breathable membranes ? By selecting materials with a better sustainability profile, such as Arkema's Advanced Bio-Circular materials.The Pebax® Rnew® family is partially produced from a renewable feedstock: castor beans.
Castor beans are a more sustainable, renewable crop that does not compete with food and does not cause deforestation.
More than just bio-based. The castor cultivation has tremendous positive impact of the farming community as it provides stable revenues to 700,000 farming families in the Gujarat region of India, where most of the world's supply originates.
Arkema is a leading driver of more sustainable castor farming in India through local actions and training programs for the farmers initiated via the Pragati Program launched in 2016.
Click here to know more about the Pragati program
Without Sacrificing on Performance
Our Pebax® Rnew® solutions for breathable membranes offer high technical performance, providing high breathability & durability.
- Adjustable Moisture Vaport Transmission Rate (MVTR)
- No loss of performance over time (no plugging)
- Good tear resistance
- Excellent virus, liquid & odor barrier
- High water entry pressure
- Free of fluorinated additives
Our Recommandation
The Pebax® Rnew® 30R51 grade for breathable membranes is 48% bio-based, free of fluorinated additives and combines top performance for optimum breathability.
it offers 30% more permeability compared to other breathable Pebax® materials in the range.
More technical information on the grade can be found here.
To go further :
See also
Back to all articles- Expertise articles
EV battery expert discusses changes and challenges in the industry
Sep 23, 2024
- White paper
More Sustainable Membrane Manufacturing for Water Filtration: Optimizing Solvent Systems for NIPS Processes
Apr 28, 2025
- Case Study
3D printed and tailor-made: orthopedic insoles made with advanced bio-circular polyamide 11
Mar 17, 2022