Sep 23, 2024 - 5 mins
EV battery expert discusses changes and challenges in the industry
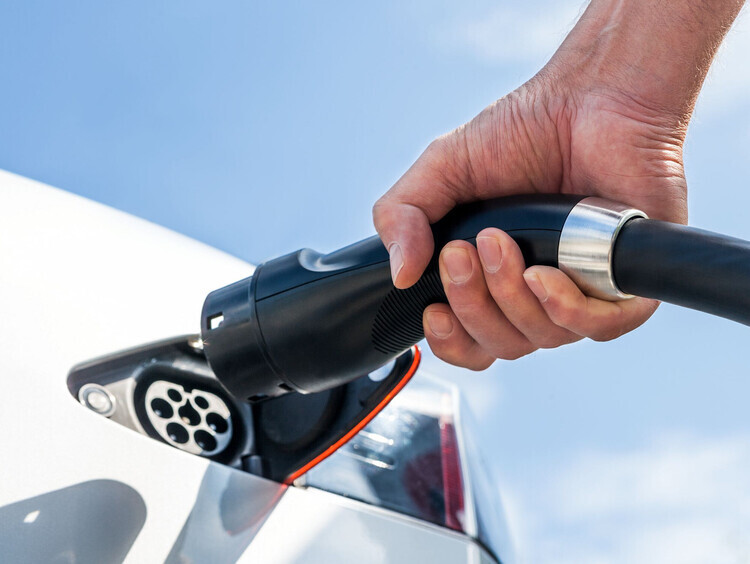
Woldemar D'AMBRIERES, Global Market Manager for Batteries at Arkema, shared his insights with EV Design & Manufacturing on How Arkema’s research into new materials and technologies supports next-generation battery development.
Specialty material producer Arkema has been working toward developing and improving materials for electric vehicle (EV) batteries for a long time.”
Navigating the Future: Challenges and Innovations in the EV Battery Industry with Arkema
What are some challenges the EV battery industry is currently facing?
The EV battery industry is facing challenges related to range, charging speed, safety, and sustainability. Despite significant advancements in the past few years, users are looking for greater range and faster charging from EV vehicles. Thermal runaway and overheating persist as safety considerations and access/availability to raw materials raises sustainability challenges.
The EV battery industry is continually making progress in all of these areas, making technology more competitive and viable every day, as electrification rates of new car sales may reach 50% by 2030 and up to 75% by 2040.
How is Arkema working to address these challenges?
CONTINUOUS INNOVATION. As new battery technologies could reach up to 50% capacities by 2040, Arkema puts strong R&D efforts to support its customers and partners in the development of sodium-ion, lithium-sulfur, solid, and semi-solid-state batteries.
RANGE. To help improve the range of EV batteries, Arkema is working directly with cell manufacturers and partners such as Proionic to increase energy density – proposing next-generation binders, such as high silicon options, and by advancing new technologies such as semi-solid and all-solid-state batteries.
CHARGING SPEED. To address charging speed, Arkema is developing specialty additives for electrolyte and carbon nanotube solutions that enhance electroconductivity.
SAFETY. In April 2024, Arkema announced an agreement to acquire a majority stake of nearly 78% in Proionic, a leading startup in the production and development of non-flammable ionic liquids. Ionic liquids are a key component for next-generation lithium-ion batteries. These new liquids developed by Proionic can significantly improve safety factors during both manufacturing and battery operations.
SUSTAINABILITY. Sustainability is the primary driver behind everything Arkema does. In the EV battery market, Arkema, through the Bostik brand, is working on new adhesive solutions enabling better recyclability and modular repairability (in other words, the ability to replace parts of the battery without having to replace the entire thing).
In addition, Arkema is constantly developing more sustainable solutions, such as biobased polyamides, to replace more traditional materials in this industry, as well as UV/LED solvent-free and low-energy intensive applications for insulation coating on the cells.
Exploring the Advantages and Innovations of Dry Manufacturing at Arkema
What are the advantages of dry manufacturing for batteries?
Dry manufacturing offers both environmental and economical benefits when compared to wet processes. Most notably, it eliminates the need for drying, which can be both space- and energy-intensive. By removing the need for a drying oven, companies can reduce both capital expenses (space, energy) and carbon footprint (energy usage) considerably.
What are some advancements Arkema has made in R&D for dry manufacturing?
Arkema is investing dedicated R&D resources in both the EU and the U.S. to test new materials in lab-scale dry manufacturing.
Additionally, Arkema has developed a range of binders specifically for dry process manufacturing, helping customers reduce their costs and improve sustainability through better energy efficiency.
Pioneering the Future: Latest Developments in EV Battery Materials by Arkema
What are some of the latest developments in materials for EV batteries?
Arkema aggressively explores new technologies and materials that support next-generation battery development. Recent activity includes:
Through the Proionic acquisition, Arkema is developing new materials, specifically ionic liquids, that are critical to advancing next-generation technologies such as semi-solid-state batteries.
In May of 2023, Arkema acquired Polytec PT, a Germany-based developer of thermal interfaces for batteries and engineering adhesives. Through this acquisition, Arkema is exploring and developing a wide range of adhesives solutions that strengthen the Bostik brand. They include innovative solutions for thermal management and recyclability.
In April of 2023, Arkema introduced a new range of Incellion sustainable waterborne acrylic solutions for high-capacity anodes, cathode primers and ceramic-coated separators inside the battery cell. Products in this new line included advanced binders, dispersants, and rheology modifiers.
In December of 2023, Arkema finalized the acquisition of a 54% stake in PI Advanced Materials (PIAM) in South Korea. Through this acquisition, Arkema supports the development of cutting-edge materials offering exceptionally high temperature resistance, dimensional stability, flexibility, and electric insulation. These include polyimide films for flexible printed circuit boards and graphite sheets used in EV batteries and other electronics.
Sustainable EV Batteries: Arkema's Innovative Materials
How can EV batteries be made more sustainable?
Sustainability drives every aspect of R&D at Arkema. As it relates to batteries, Arkema is focusing on five key areas:
- Proposing waterborne solutions to replace solvent based solutions.
- Alternative and lower carbon feedstocks, through the introduction of waterborne and biobased alternatives to traditional materials.
- Lowering energy intensity, by supporting dry process manufacturing.
- Improving end of life management with materials that can be more easily recycled or replaced without having to scrap the entire battery.
- Extending durability product life, by introducing materials that improve the performance of the battery, including better thermal control, charge time, and range.
What kind of materials does Arkema offer for batteries?
Arkema has been producing materials for EV batteries since the 1990s.
The company’s current product line includes solutions for polymers for separator coating, electrolyte salts, cathode binders, acrylic rheology modifiers, resins, and photoinitiators for UV curable dielectric coatings, smart adhesives and sealants, thermoplastic composites, encapsulating case coatings, battery management systems, immersion cooling systems, busbar coatings, encapsulating and molding electronic components, piezoelectric polymers, and more.
How are these materials different from the materials commonly used for EV batteries?
Arkema is taking a forward-thinking approach to EV battery solutions. We are a specialty materials company and choose to focus on addressing the specific needs of our customers rather than as a large-volume commodity manufacturer.
This is also the unique combination of all Arkema solution portfolios which enables innovation and a strong go-to partner for the EV leaders across the globe.
This focus allows us to identify both new products and potential technology acquisitions worldwide that will advance the science of EV battery design and position Arkema as a leader in the industry.
Is there anything else you would like us to know?
Arkema is one of the longest-standing producers of specialty materials in the market. The company has been supplying the industry for almost as long as it has existed. We have R&D and production in all major geographies where EV batteries are products, including the Americas, Europe and Asia, giving us the ability to support customers locally with both product and development support, while still addressing the global needs of these applications.
Discover Arkema's material offering for batteries
See also
Back to all articles- White paper
- Case Study
- Expertise articles