Sep 16, 2024 - 3 mins
Arkema’s central hub for battery material expertise
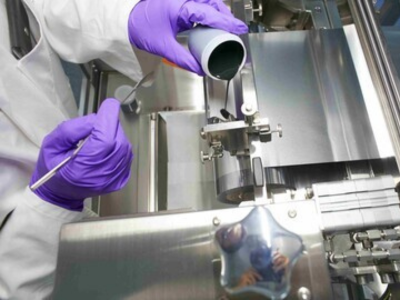
Global demand for batteries is increasing, driven largely by the imperative to reduce climate change through the electrification of mobility and the broader energy transition. At the same time, batteries must be safer, more efficient, more sustainable, and affordable to facilitate this shift.
Expanded in 2021, Arkema’s Battery Center, in Lyon, plays a key role in this transition and strives to develop high-performing materials for current lithium cell technologies as well as next-generation batteries, such as semi-solid, solid and sodium. Closely connected with other research centers, in Asia and the USA, the center is equipped with cutting-edge technologies allowing battery manufacturers to leverage reliable and real-life data to speed up the development of the next generation of batteries.
Boosting performances of batteries
The Christian Collette Center of Excellence focuses on enhancing the performance of anode, cathode, separator and electrolyte. Our experts are constantly developing our materials to provide optimal processability, mechanical integrity, electrochemical performance, and safety. Like the most advanced giga factories, the center has state-of-the-art equipment that enables our teams to test our product at every stage of the battery production process from slurry formulation to testing, to cell assembly in “dry room conditions”.
Cathode: Kynar® PVDF, the industry reference
The expertise in battery cathode technology is a cornerstone of the Center of Excellence, focusing on continuously improving materials for both anodes and cathodes to ensure uniformity and high-quality performance. The electrode manufacturing process begins with the mixing of active materials, binders, and conductive agents to create a homogeneous slurry, a critical step in obtaining the slurry with a controlled viscosity. The center of excellence operates a state-of-the-art dry room with coating and drying equipment to further advance our cathode expertise. It is also the home of Arkema’s Kynar® PVDF material which became an industry reference for its high electromechanical resistance, high purity, mechanical stability and advantages in processing.
Anode: towards high silicon rates with Incellion™
High silicon content batteries increase the energy density of batteries. Incellion™ acrylic based solutions are developed to enable the adoption of this technology by overcoming the challenge of volume expansion of silicon during charging.
Separator: safer and always thinner
The separator is a critical component that prevents short circuits while allowing ion flow between the anode and cathode. The center's expertise focuses on slurry viscosity and homogeneity for effective coating application at the near-industrial level. Adhesive and separator coating layer materials and binders such as Kynar® PVDF and Incellion™ acrylic based solutions highlight Arkema’s expertise in the separator application. Our product research focuses on developing solutions to improve the cohesion of the separator with the electrodes and to increase thermal resistance.
Electrolyte
The electrolyte is crucial for ion transport within the battery cell. Our R&D in this domain focuses on boosting ion transport with our Foranext® Ultra-pure LiFSI salt and LiTDI additives. The objective is to develop custom electrolyte solutions tailored to specific cell chemistries, optimizing ionic conductivity and stability for the next-generation batteries. Discover the center activities in the video below.
Unique battery cell testing set-up
Arkema offers advanced materials solutions for battery applications and has also developed a unique expertise in battery cell testing at the Christian Collette Center of Excellence. The center can make and test single-cell coin and pouch cells in real conditions, up to 2 ampere/hour. Our experts perform various tests to check the lifecycle and the charging and ageing behavior of batteries due to unfavorable operating conditions such as temperature, power demand and mechanical integration. This unique testing set-up allows us to find materials solutions for industrial-level cell manufacturing problems by getting insights from real-life tests.
The Center of Excellence also collaborates with partners along the battery value chain to address industrial challenges and sustainability goals.
Battery recycling
As the demand for batteries is planned to grow quickly in the coming years, the industry needs to adopt circular practices to reduce waste and environmental impact. Arkema fosters collaboration in research and development to respond to material challenges in sustainability. The center collaborates with various industry actors and research institutes on the French national and EU levels to share knowledge with a holistic approach to battery recycling.
The Rhinoceros project
The Rhinoceros project, involving a consortium including Tecnalia, Accurec, JGI Hydrometal, and others, aims to investigate circular recycling routes for NMC batteries (nickel-manganese-cobalt)
The goal is to recover various materials such as metals, graphite, fluorinated compounds, electrolytes, polymers, and active.
The Reuse project
The Reuse project, in collaboration with Kyburz, Morrow Batteries, Imerys, and other leading EU research institutes, focuses on improving the circularity and sustainability of the entire LFP ( battery waste stream. This project seeks to develop new recycling processes to maximize the recovery of elements and components from production scrap to end-of-life LFP (lithium, iron, phosphate) LiB batteries.
Towards new technologies
Arkema is at the forefront of advancing next-generation battery technologies through its R&D efforts, focusing on innovative materials for gel polymer electrolytes, sodium-ion batteries, solid-state sulfides, and polymer conductors. By investing in gel polymer electrolytes.
Arkema aims to enhance the safety and performance of batteries, offering a flexible yet stable medium for ion transport. Our work on sodium-ion batteries addresses the need for more sustainable and cost-effective alternatives to lithium-ion systems, leveraging the abundance and lower cost of sodium.
See also
Back to all articles- Expertise articles
- White paper
- Case Study