Dec 13, 2024 - 3 min
Orgasol® PA12 3D printing powders: Outstanding powder recyclability and surface aesthetics
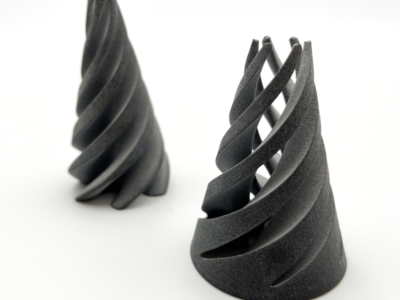
In the rapidly evolving field of 3D printing, material innovation is key to unlocking new possibilities. At Arkema, we have developed new Orgasol® PA12 solutions, groundbreaking powders designed specifically for Powder Bed Fusion 3D printing technologies. This article highlights the unique value proposition of Orgasol® PA12, demonstrating its potential to transform the 3D printing landscape.
A Game-Changer for Powder Bed Fusion 3D Printing
Orgasol® PA12 powders stand out as a game-changer for PBF technologies, offering unmatched aesthetics and cost-efficiency. Its superior properties enable manufacturers to produce parts with exceptional surface quality while reducing post-processing time and cost.
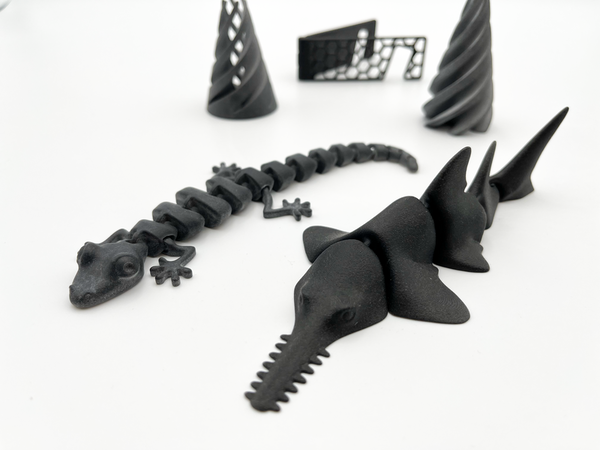
PA12 Powder: Cost reduction and efficiency
One of the most compelling advantages of Orgasol® PA12 is its ability to significantly reduce variable and total printing costs thanks to high recyclability and nesting optimization enablement. As a few orders of magnitude, below are the savings that can be achieved using Orgasol® PA12-based solutions on different PBF 3D technologies. More precise calculations depending on the user’s machine, nesting density per job, internal costs etc. can be deepened case by case.
HP Technology:
- Reduce variable printing costs by up to 50% (minimum 10%)
- Reduce total printing costs by up to 40% (minimum 5%).
- Reduce lead time by up to 30%.
SLS Technology:
- Reduce variable printing costs by up to 50% (minimum 20%).
- Reduce total printing costs by up to 30% (minimum 15%).
These reductions translate into substantial savings and increased production efficiency, making Orgasol® PA12 an economically attractive option for parts manufacturers
PA12 3D-printed Parts: Enhanced Surface Aesthetics
Orgasol® PA12 enables the production of smoother parts with improved surface aesthetics. This is particularly beneficial for applications where visual and tactile quality are paramount. The material’s fine particle size and uniform distribution contribute to its ability to produce high-quality finishes.
The scientific article “Influence of the Origin of Polyamide 12 Powder on the Laser Sintering Process and Laser Sintered Parts”1 highlights key differences between various PA12 powders.
Figure 1. shows SEM images for two investigated PA powders. The size distribution and morphology of usual PA12 consist of relatively spherical particles with a narrow size distribution of around 60 µm. It is the result of a solution–precipitation process in ethanol. The image on the right highlights an Orgasol® PA12 powder that consists of smooth, near-spherical particles, with a particle size distribution of around 40 µm. The main difference from usual PA12 powders is the uniqueness of the Orgasol® PA12 manufacturing process: Direct polymerization.
These attributes directly impact the surface of 3D-printed parts with improved aesthetics. These sensorial benefits also explain why these powders have been widely used in the field of decorative cosmetics, improving spreading and providing easy glide-on application.
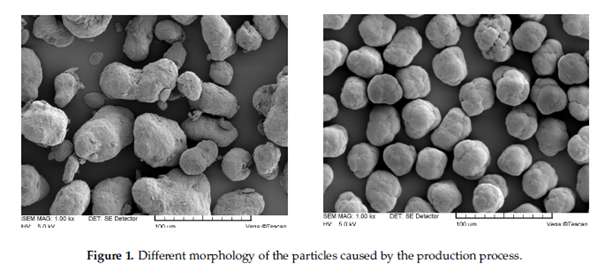
Sustainability and Zero-Waste Solution in 3D Printing
In addition to its economic and aesthetic benefits, Orgasol® PA12 drives sustainability in 3D printing. The material supports a zero-waste solution thanks to the powder’s game-changing reusability, aligning with the growing demand for environmentally responsible manufacturing practices. Its recyclability ensures that waste is minimized, contributing to a more sustainable production process.
The scientific article “Characterization of polyamide powders for determination of laser sintering processability”2 highlights the viscosity stability of Orgasol® PA12 powders. Figure 2. shows that usual PA12 powders show significant polycondensation behavior, especially at higher temperatures, with substantial viscosity increases. Orgasol® PA12, on the other hand, shows no change in viscosity at all. Only at the highest investigated temperature, a negligible increase is visible.
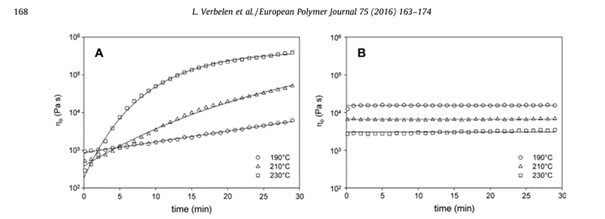
This reusability advantage comes along with its improved repeatability. Unlike other materials that degrade over time, Orgasol® PA12 maintains its properties, ensuring consistent performance across multiple production cycles. This stability is crucial for applications requiring high precision and reliability.
The scientific article “A review of aging, degradation, and reusability of PA12 powders in selective laser sintering additive manufacturing”3 highlights the stability, that enables it to reach top-level reusability with Orgasol® PA12. While PA12 usually viscosity increases with ageing, Orgasol® PA12 shows high stability.
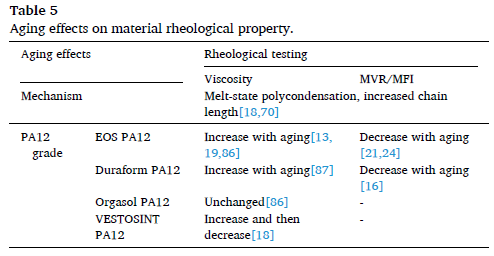
Unparalled benefits of Orgasol® PA12
Orgasol® PA12 represents a significant advancement in 3D printing materials, offering unparalleled benefits in terms of cost-efficiency, surface quality, sustainability, and repeatability. As the industry continues to evolve, materials like Orgasol® PA12 will play a crucial role in driving innovation enabling new applications and growing the additive manufacturing market.
Sources:
- Manfred Schmid, Rob Kleijnen, Marc Vetterli and Konrad Wegener, “Influence of the Origin of Polyamide 12 Powder on the Laser Sintering Process and Laser Sintered Parts”, Applied Science, 2017
- Leander Verbelen, Sasan Dadbakhsh, Michael Van den Eynde, Jean-Pierre Kruth, Bart Goderis, Peter Van Puyvelde, “Characterization of polyamide powders for determination of laser sintering processability”, European Polymer Journal, Volume 75, 2016
- Feifei Yang, Navid Zobeiry, Ramulu Mamidala, Xu Chen, “A review of aging, degradation, and reusability of PA12 powders in selective laser sintering additive manufacturing”, Materials Today Communications, Volume 34, 2023
See also
Back to all articles- Expertise articles
- White paper
- Case Study