Our commitment to reducing carbon footprint
Reducing the Carbon Footprint of Bio-Based Polyamide 11 Global Production
There are several parameters to consider in order to improve the carbon footprint figures. Currently, Arkema provides an unconditional carbon footprint value for polyamide 11 of 1.3 kg CO₂ per unit. What sets our approach apart?
Product range: Applies to all Amino 11 monomers and Rilsan® PA11* global production
Geographical Coverage: Global
Energy Usage: Renewable energy for manufacturing processes
*All our polymers containing Amino 11 are considered in this range, for more detailed carbon footprint information on other products please reach out to us.
Process: 100% segregated bio-based PA11 production;
Feedstock: Castor oil – no compromise on ethics or environmental impacts such as deforestation, food competition, ethical labor conditions, fair trading;
Allocation: No feedstock mass balance allocation
Cost: No price premium for sustainability improvements
Evaluating Carbon Footprint in Lifecycle Assessment (LCA)
As a material producer, we assess the impact of our materials within the cradle-to-gate perimeter of the product lifecycle. Scope 3 Upstream includes impacts starting from the castor plant and to other materials used in the transformation process into polymers. Thanks to Arkema’s active collaboration with castor farming communities, we have reliable agricultural data from the fields.
Arkema's key actions to further reduce the carbon footprint include:
- Using renewable resources such as raw materials (bio-based and/or recycled) and/or energy for production
- Improving our processes
- Optimizing freight
- Collaborating with suppliers
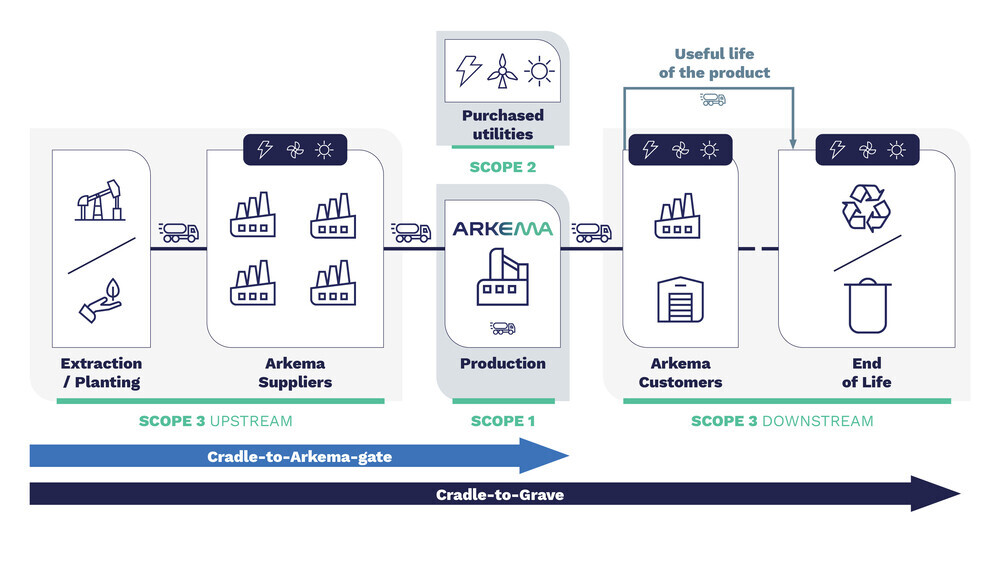
1.3 kg CO₂e/kg of Polyamide 11
In Polyamide 11 production chain, Arkema uses bio-based raw materials coming from the castor plant. This is the main contributor to reduced carbon emissions vs fossil-based polyamides coming from scope 3 Upstream.
From January 2023, Arkema signed an agreement for 300 GWh/year of renewable biomethane energy supply with ENGIE, to further reduce the carbon footprint of its bio-based materials. Biomethane is a renewable alternative to natural gas with a lower carbon footprint and is produced through the fermentation of organic matter.
Following the announcement in 2023 of reducing the carbon footprint to less than 2 kg of CO2 of our Polyamide 11, we implemented renewable electricity throughout our plants. Now we have achieved a new milestone for our castor-based Rilsan® PA11, from the beginning of 2025 the carbon footprint will reach 1.3 kg of CO2 per kg of product according to ISO14040, 14044 and 14067 standards.
Our approach to Lifecycle Assessment (LCA)
In-house LCA expertise
Arkema has an in-house team dedicated to Life Cycle Assessment and Sustainability Methods. The team includes LCA expert practitioners who also participate in several international working groups.
Our approach to calculating the cradle-to-gate carbon footprint is transparent and independently audited with renewed certifications. We calculate the product carbon footprints according to ISO 14040:2006, ISO 14044:2006, ISO 14067:2018 standards.
System boundaries
We defined our system boundaries as cradle-to-gate and we consider all processes from raw material extraction (cradle) to the factory gate (before the product is shipped to the customer). We ensure no significant cut-offs, which implies that all inputs and outputs contributing to less than 5% of the total mass and energy are included.
We use 1 kg of product manufactured by Arkema as a functional unit to provide a consistent basis for measuring and comparing the environmental impacts of our products.
Data source and tools
In LCA calculations, our team relies on primary data sourced directly from Arkema sites information, as well as relevant secondary data for upstream flows sourced from reputable LCA reference databases, including Ecoinvent v3.9 and Plastics Europe.
The life cycle assessment (LCA) is performed using an up-to-date version of SimaPro® software. We apply the IPCC 2021 GWP 100 method, which includes CO2 uptake, to calculate the net global warming potential of our products over a 100-year time horizon. This ensures that our carbon footprint calculations are regularly updated according to the latest and most comprehensive global warming potential data.
Comprehensive Lifecycle Assessment: Beyond Carbon Footprints
In the Lifecycle Assessment (LCA), we calculate not only the carbon footprint but also other impacts such as acidification, eutrophication, and resource depletion. This multi-criteria assessment ensures a more comprehensive comparison of materials. Care should be taken in interpreting and analyzing trade-offs between impact categories. For instance, comparisons between bio-based and fossil-based materials may favor fossil-based materials depending on the indicator considered (water use), which might not be justified from a broader perspective.
Another example: some factors such as food competition and social benefits are not clearly evaluated in LCA. Our Advanced Bio-Circular (ABC) materials approach addresses a broader picture to support our customers in their material decision-making process towards more sustainable solutions.