The ZEBRA (Zero wastE Blade ReseArch) project marks a significant leap forward in the recycling and circular economy for wind turbine blades. This collaborative effort demonstrates a breakthrough in the complete recycling of thermoplastic blades achieving significant environmental and economic benefits.
A Consortium of Leading Companies Drives Innovation
The ZEBRA project is a unique partnership led by the French Institute for Technological Research, IRT Jules Verne. Joining forces are industry leaders Arkema (resin supplier), Owens Corning (glass fiber supplier), LM Wind Power (blade manufacturer), SUEZ (dismantling and waste processing), CANOE R&D center (recycling technology), and ENGIE (life cycle analysis).
Each company played a crucial role in the development of the closed-loop recycling process:
- Arkema developed and validated the generation of recycled Elium® monomer through thermolysis, and, together with its subsidiary Bostik, an innovative adhesive for the blade assembly that is recycled together with Elium® paving the way for industrial-scale implementation.
- Owens Corning successfully recovered glass fiber at pilot scale, enabling its reintroduction into the production process for their Sustaina® product line.
- LM Wind Power manufactured two wind turbine blades with Arkema’s Elium® resin and Owens Corning’s Ultrablade® fabrics; one blade including a large structural element made with recycled Elium® resin.
- SUEZ provided cutting and grinding expertise for processing the blades.
- CANOE R&D center optimized recycling for production and carbon blade waste, additionally developing methods for repurposing waste streams through mechanical recycling.
- ENGIE conducted a comprehensive life cycle analysis demonstrating the environmental benefits of closed-loop ZEBRA blades and validated their economic viability.
A Sustainable Future for Wind Energy
The ZEBRA project successfully recycled Elium® resin and Ultrablade® fabrics from wind turbine blades and manufacturing waste, reformulating them back into usable materials. This closed-loop process addresses the growing challenge of end-of-life blade management within the wind energy industry.
- Recycled Elium® Monomer: Arkema achieved a yield of over 75% in the thermolysis process, paving the way for industrial-scale production of recycled resin.
- Recovered Glass Fiber: Owens Corning successfully retrieved glass fiber for remelting and reintegration into their Sustaina® product line.
- Life Cycle and Cost Analysis: ENGIE's study confirmed the significant environmental benefits and economic viability of ZEBRA blades when assuming a closed-loop recycling system from production to end-of-life.
ZEBRA blade using Elium® thermoplastic resin, Bostik’s highly compatible adhesive and Ultrablade® fabrics is bringing the best closed-loop recycling solution compared to traditional thermoset system. The operating cost and investments for recycling facility are significantly lowered. The CO2 emission linked to the recycling operations is reduced as well. All those results are making the closed-loop recycling solution of ZEBRA blades a viable option both on economic and environmental standpoints.
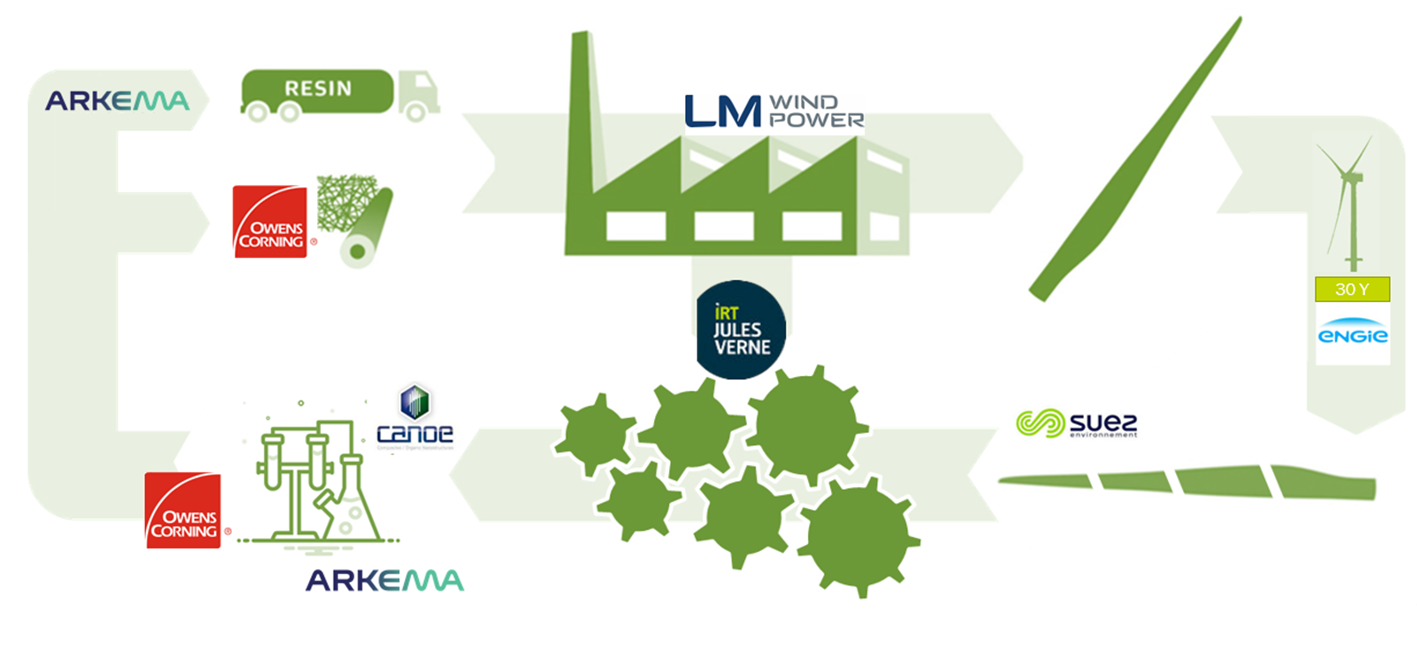
CANOE is a French R&T provider, specialized in polymer formulation, fiber-reinforced composite manufacturing and recycling process development, recycled fiber reprocessing, sensor integration for SHM, materials characterization and non-destructive testing. CANOE provides R&D services to companies over the whole manufacturing chain value of a composite part from design and prototyping up to pre-series and industrialization assistance.
ENGIE is a global reference in low-carbon energy and services. With its 97,000 employees, clients, partners and stakeholders, the Group strives every day to accelerate the transition towards a carbon-neutral economy, through reduced energy consumption and more environmentally friendly solutions.
Inspired by its purpose statement, ENGIE reconciles economic performance with a positive impact on people and the planet, building on its key businesses (gas, renewable energy, services) to offer competitive solutions to its clients.
Turnover in 2023: €82.6 billion. The Group is listed on the Paris and Brussels stock exchanges (ENGI) and is represented in the main financial indices (CAC 40, Euronext 100, FTSE Euro 100, MSCI Europe) and non-financial indices (DJSI World, Euronext Vigeo Eiris - Europe 120 / France 20, MSCI EMU ESG screened, MSCI EUROPE ESG Universal Select, Stoxx Europe 600 ESG-X).
IRT Jules Verne is a mutualized industrial research centre dedicated to manufacturing. Working closely with production equipment manufacturers and integrators, IRT Jules Verne caters to 4 strategic industrial sectors: aeronautics, shipbuilding, the automotive industry, and renewable marine energy. The IRT team works hand in hand with the very best industrial and academic resources in the manufacturing field.
Its vocation is to improve the competitiveness of strategic industrial sectors in France by creating disruptive technologies for manufacturing processes. Its mission is to speed up innovation and technology transfer to factories. In its bid to provide comprehensive solutions up to scale-1 demonstrators, IRT Jules Verne installs and utilises a wide range of exclusive state-of-the-art equipment.
The IRT Jules Verne receives state aid under the Future Investments program with reference number ANR-10-AIRT-02
LM Wind Power, a GE Vernova business, is an industry-leading developer and manufacturer of high-quality rotor blades for onshore and offshore wind turbines with blade services solutions and a global manufacturing footprint, headquartered in Denmark.
LM Wind Power has produced over 270,000 blades since 1978, corresponding to 152 GW installed capacity and mitigation of 332 million metric tons of CO2-emission. As part of the its sustainability journey, LM Wind Power became the first carbon neutral company in the wind industry in 2018 and is committed to building Zero Waste Blades by 2030.
Owens Corning is a global building and construction materials leader committed to building a sustainable future through material innovation. Our four integrated businesses – Roofing, Insulation, Doors, and Composites – provide durable, sustainable, energy-efficient solutions that leverage our unique material science, manufacturing, and market knowledge to help our customers win and grow.
We are global in scope, human in scale with more than 25,000 employees in 31 countries dedicated to generating value for our customers and shareholders, and making a difference in the communities where we work and live. Founded in 1938 and based in Toledo, Ohio, USA, Owens Corning posted 2023 sales of $9.7 billion.
SUEZ is a major player in environmental services. For almost 160 years, SUEZ has supported local communities and industrial companies in the management of essential services such as water, waste, and air quality.
As such, SUEZ produces drinking water for 66 million people worldwide, recovers 2 million tons of secondary raw materials per year, and generates 3.1 TWh of renewable energy from waste. In our ongoing management of the ecological transition and climate change challenges, SUEZ relies on the expertise and commitment of its 35,000 employees (particularly in France, Italy, Central Europe, Africa, Asia, and Australia) to offer high value-added and customized environmental solutions to all its customers. SUEZ’s expertise allows, for instance, its customers to avoid the emission of 4.2 million tons of CO2, thus improving their carbon footprint and their impact on climate. With a turnover of nearly 7 billion euros and backed by its expertise and capacity to innovate, SUEZ has strong growth prospects.
SUEZ relies on a solid consortium of investors made up of Meridiam and GIP – with 40% stakes each - and the Caisse des Dépôts et Consignations Group with a 20% stake in the capital, including 8% held by CNP Assurances, to pursue its strategic development plans in France and internationally.